
Integrating an Order Management (OMS) in your Supply Chain Management (SCM): a comprehensive guide
In today’s complex and rapidly evolving business landscape, effective supply chain management (SCM) is the linchpin that holds everything together. At the heart of SCM lies the Order Management System (OMS), a crucial component that streamlines the flow of goods, information and services.
In this comprehensive guide, we will explore the significance of SCM and OMS, their roles in commerce today, and how integrating these systems can revolutionise your operations.
Table of contents
1. What is Supply Chain Management?
i. Definition
ii. Importance in modern business
iii. Key elements of SCM
2. Understanding the Order Management System (OMS)
i. What is OMS?
ii. Role in SCM
iii. Benefits and functions
3. The supply chain process
i. Planning and strategy
ii. Procurement and sourcing
iii. Manufacturing and production
iv. Logistics and delivery
4. The intersection of SCM and OMS
i. How OMS supports SCM
ii. Inventory management
iii. Order processing
iv. Customer service
5. Implementing OMS within SCM
i. Technology requirements
ii. Integration steps
iii. Success stories
6. Challenges in Supply Chain Management
i. Common obstacles
ii. Role of OMS in overcoming challenges
iii. Tips and strategies
7. Trends and future of SCM and OMS
i. Emerging technologies
ii. Impact of globalisation
iii. Sustainability considerations
8. Conclusion
i. Recap of SCM and OMS integration
ii. Best practices
iii. Future perspectives
1. What is Supply Chain Management?
Definition
Supply Chain Management (SCM) is the strategic orchestration of goods, data and finances related to a product or service. Supply chain activities encompass production, procurement, inventory planning, logistics and order management. SCM is the art of connecting the dots in a complex network that spans from suppliers to customers, optimising each step along the way.
Importance in modern business
In today’s global marketplace, SCM holds immense importance for several reasons:
- Efficiency: It enhances operational efficiency by minimising waste, reducing fulfilment times and ensuring the optimal utilisation of resources.
- Cost reduction: Effective SCM can lead to substantial cost savings through efficient production processes, optimised inventory management and streamlined logistics.
- Customer satisfaction: SCM helps businesses meet their customers’ demands promptly, resulting in higher satisfaction and brand loyalty.
- Competitive advantage: A well-structured supply chain allows businesses to respond swiftly to market changes and outperform competitors at each stage of the customer journey.
- Global reach: In an era of globalisation, SCM empowers businesses to expand their reach and venture into new markets.
Key elements of SCM
Supply Chain Management comprises several key elements that each play a crucial role in the broader supply chain:
- Planning: Forecasting demand, setting objectives and developing strategies to achieve them.
- Sourcing: Identifying and selecting suppliers, negotiating contracts and ensuring a consistent supply of goods.
- Manufacturing: Transforming raw materials into finished products efficiently and cost-effectively.
- Fulfilment: Managing the transportation, warehousing and distribution of goods to customers.
- Reverse logistics: Taking back products that are defective, unwanted or unsold.
Now, let’s delve into the world of Order Management Systems (OMS) to understand how they complement SCM.
2. Understanding the Order Management System (OMS)
What is an OMS?
An Order Management System (OMS) is a software solution that helps businesses manage and automate the entire order lifecycle, from order creation to order fulfilment. It acts as the digital conductor that orchestrates and optimises all order-related processes.
Role in SCM
An OMS plays a crucial role in SCM by bridging the gap between customer demand and supply chain execution. It ensures that inventory is managed effectively, orders are processed efficiently and customers receive what they expect when they expect it.
Benefits and functions
Here are some key benefits and functions of OMS:
- Order processing: An OMS automates order entry, validation and processing, reducing manual errors and processing times.
- Inventory management: It provides real-time visibility into inventory levels, helping businesses maintain optimal stock levels to avoid overstocking or stockouts.
- Customer service: An OMS enhances customer satisfaction by providing accurate order status information and facilitating easy returns and exchanges.
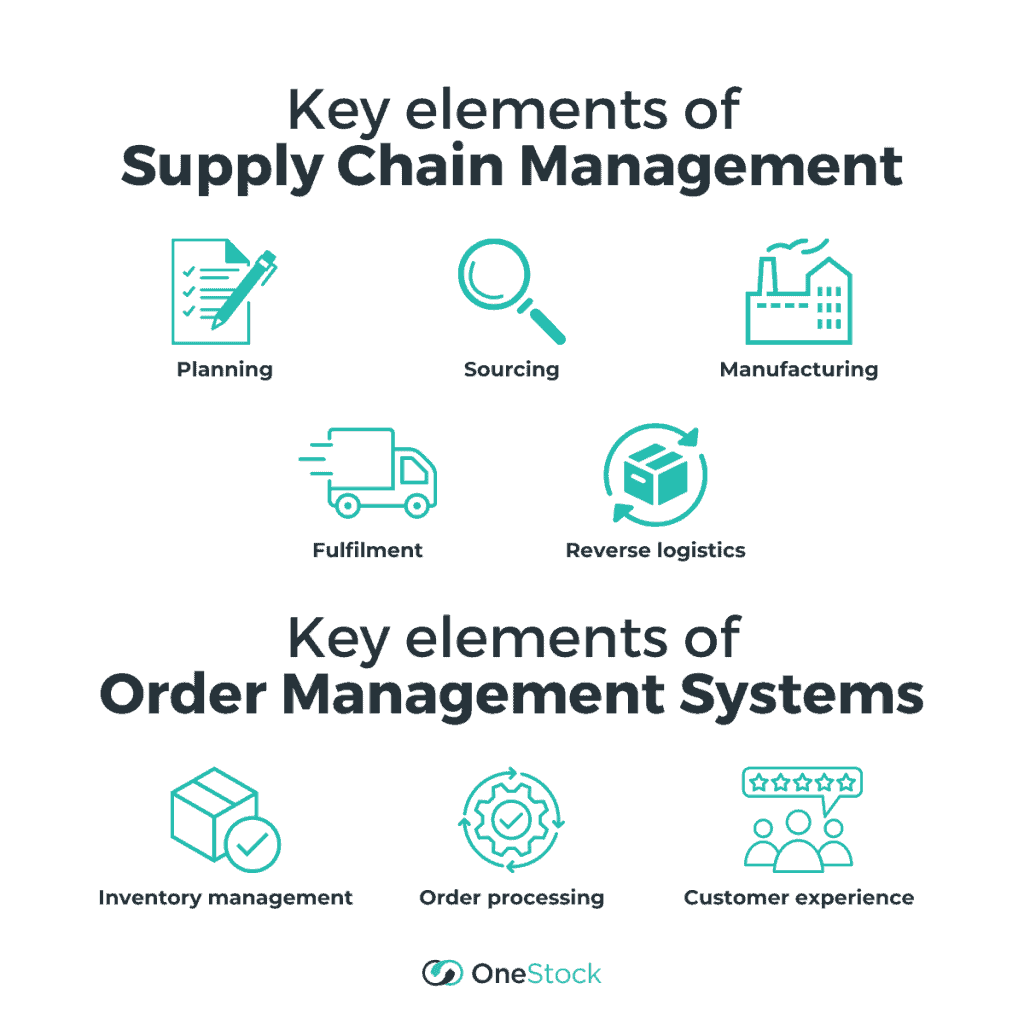
With a clear understanding of SCM and OMS, we’re ready to explore the supply chain process and how these systems intersect.
3. The supply chain process
Effective supply chain management involves a series of interconnected processes that work together seamlessly to deliver products and services to customers. These processes can be categorised into four main phases:
Planning and strategy
- Demand forecasting: Accurately predicting customer demand to ensure adequate stock levels.
- Strategic planning: Developing long-term strategies and goals for the supply chain.
- Risk management: Identifying and mitigating potential risks that could disrupt the supply chain.
Procurement and sourcing
- Supplier selection: Choosing reliable suppliers who can provide quality materials at competitive prices.
- Contract negotiation: Negotiating favourable terms and conditions with suppliers.
- Order placement: Placing orders for raw materials or products based on demand.
Manufacturing and production
- Production planning: Scheduling production to meet demand while minimising costs.
- Quality control: Ensuring the quality of products through inspections and testing.
- Optimisation: Streamlining production processes for efficiency.
Logistics and delivery
- Warehousing: Managing storage facilities efficiently to reduce holding costs.
- Transportation: Planning and executing the movement of goods from production facilities to distribution centres and customers.
- Order fulfilment: Processing customer orders and picking, packing and shipping products.
4. The intersection of SCM and OMS
Now, let’s explore how the Order Management System intersects with SCM and enhances these processes.
How an OMS supports SCM
An OMS plays a pivotal role in various aspects of SCM:
Inventory management
- Real-time visibility: An OMS provides real-time insights into inventory levels, helping businesses make informed decisions about restocking and replenishment.
- Optimisation: It helps optimise inventory turnover rates by ensuring that products are in stock when and where needed, reducing carrying costs.
Order processing
- Automation: An OMS automates order processing, reducing errors and speeding up the fulfilment process.
- Order tracking: Customers can track their orders in real-time, improving transparency and customer satisfaction.
Customer service
- Returns and exchanges: An OMS facilitates the smooth handling of returns and exchanges through any channel, enhancing the overall customer experience.
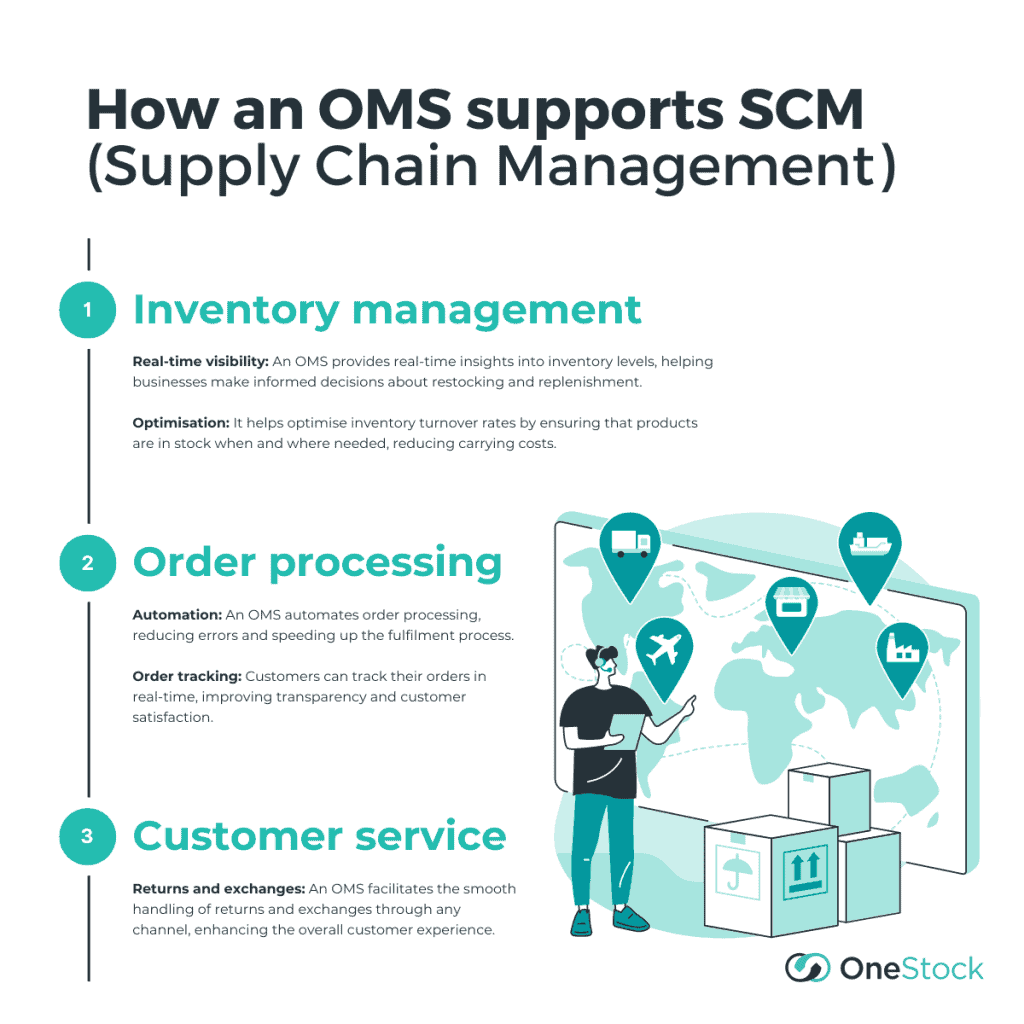
With the benefits of integrating OMS within SCM apparent, let’s explore how to implement OMS successfully.
5. Implementing an OMS within SCM
Technology requirements
To implement an Order Management System within SCM, businesses need the following technology components:
- OMS software: Choose a robust, best-of-breed OMS software that aligns with your business needs and integrates seamlessly with your existing systems.
- Integration middleware: Middleware solutions are essential for connecting an OMS with other systems such as Enterprise Resource Planning (ERP) and Customer Relationship Management (CRM) systems.
Integration steps
- Assessment: Evaluate your current SCM processes and identify areas where an OMS can add value.
- Vendor selection: Choose a reputable OMS vendor (like OneStock!) and ensure their software aligns with your company’s specific requirements.
- Integration planning: Develop a detailed integration plan, including timelines and resource allocation.
- Testing: Thoroughly test the OMS integration to identify and rectify any issues.
- Training: Train your staff on how to use the new OMS effectively.
Success stories
Many businesses have successfully integrated an OMS within their SCM processes, resulting in improved efficiency and customer satisfaction:
- Online home improvement retailer ManoMano uses an OMS for the management of inter-warehouse flows, ensuring the right amount of inventory is available in each of its warehouses to fulfil customer orders at speed.
- Würth is a global wholesaler supplying components to trade and industry, and uses an OMS to easily connect customers to its thousands of references through Click & Collect and Reserve & Collect services across 180 stores.
- Digital entertainment group Webedia uses an OMS to effectively manage stock and orchestrate customer orders from its e-commerce sites and marketplaces like Amazon, optimising its supply chain while meeting customer expectations for delivery.
6. Challenges in Supply Chain Management
Despite the numerous benefits, SCM can be fraught with challenges. Let’s examine some common obstacles and the role of an OMS in overcoming them.
Common obstacles
- Supply chain disruptions: Natural disasters, political instability and other unforeseen events can disrupt the supply chain. An OMS can help mitigate these disruptions by providing real-time visibility and enabling rapid response.
- Inventory management: Maintaining the right level of inventory can be challenging. An OMS helps businesses optimise stock levels to reduce carrying costs associated with excess inventory and missed sales due to stockouts.
- Customer expectations: Meeting customer expectations for fast delivery and excellent service can be a difficult task. An OMS streamlines order processing, enables new fulfilment options and enhances customer service.
Tips and strategies
- Data analytics: Leverage data analytics to gain insights into your supply chain and make data-driven decisions.
- Collaboration: Work closely with suppliers, wholesalers and logistics partners to improve communication and coordination.
- Continuous Improvement: Continuously evaluate and refine your SCM processes to adapt to changing market conditions.
7. Trends and future of SCM and OMS
As technology evolves and the business landscape changes, SCM and OMS are also evolving. Here are some trends shaping the future of SCM and OMS:
Emerging technologies
- Blockchain: Enhances transparency and traceability in the supply chain.
- Artificial Intelligence (AI) and Machine Learning: Improve demand forecasting and optimise supply chain operations.
- Internet of Things (IoT): Provides real-time data on the location and condition of goods.
Impact of globalisation
As businesses expand globally, SCM and OMS will play a pivotal role in managing complex international supply chains and meeting diverse customer demands.
Sustainability considerations
Sustainability is becoming a critical factor in SCM and the OMS. Businesses are focusing on eco-friendly sourcing, transportation and packaging to reduce their environmental footprint.
8. Conclusion
In conclusion, Supply Chain Management (SCM) and the Order Management System (OMS) are integral components of modern business operations. Integrating an OMS within SCM can streamline processes, enhance efficiency and improve customer satisfaction.
To succeed in this endeavour, businesses must carefully evaluate their technology requirements, plan integration meticulously, and stay attuned to emerging trends and challenges in the ever-evolving world of SCM and OMS.
Recap of SCM and OMS integration
- SCM involves the strategic coordination of processes from planning to delivery.
- An OMS streamlines order processing, inventory management and customer service.
- Successful integration requires the right technology, planning and training.
Best practices
- Leverage data and technology for real-time insights.
- Collaborate with partners for a more efficient supply chain.
- Continuously improve processes to adapt to changing market conditions.
Future perspectives
- Emerging technologies like blockchain, AI and IoT will shape the future of SCM and OMS.
- Globalisation and sustainability considerations will drive changes in supply chain management.
By embracing these principles and harnessing the power of SCM and OMS integration, businesses can stay competitive, resilient and responsive to the ever-changing demands of modern commerce.